Wood processing
In one of the world’s oldest industrial sectors, safety, productivity, and maximum yield from raw materials are vital parameters. The use of timber in construction is increasing, and wood products are in high demand. Malfunctioning production equipment can directly affect throughput and may impact the entire supply chain. Keeping expensive and complex equipment running safely and with minimal disruption is essential to maintaining an efficient operation.
With its exceptionally high production pace, process and quality improvements are the keys to higher profit in this industry. The production equipment in sawmills – with sharp blades, sawdust, and heat-generating machinery – creates a multi-hazard environment. Staying on top of maintenance needs to prevent unplanned downtime and personal injury is critical. Early warnings of machine problems help reduce the risk of breakdowns and increase plant and operator safety.
"The purpose of our investment has always been to avoid corrective maintenance as much as possible, to allow ourselves to plan the right maintenance effort at the right time, and thus work proactively and preventively.
Unplanned stops in the major drives in the process can take anything from one to several shifts to rectify, which results in major production loss, which is difficult to catch up on since more or less everything we produce are sold products. With the measurement system, we can maintain higher machine availability and better profitability.
The investment has already started to pay off as we have avoided replacing a large part of the production site in conjunction with a major breakdown. This was possible because extra control measurements could be performed via the measurement system. These measurements showed good values, giving us a decision basis to avoid unnecessary replacement of process parts.
Another significant advantage, or security, that the system provides is increased safety in the form of reduced risk of fire in the event of bearing failure, which is otherwise something that we in the industry have great respect for."
Joakim Jonasson, Maintenance Manager Mechanics at Norra Timber
Condition monitoring applications in wood processing
Typical condition monitoring targets are production-critical equipment, expensive or hard-to-repair assets, and machines causing downtime in case of failure, such as:
- Sawlines
- Blowers
- Debarkers
- Trimmers
- Edgers
- Planers
- Log reducers
- Motors
- Wood chippers
- Fans
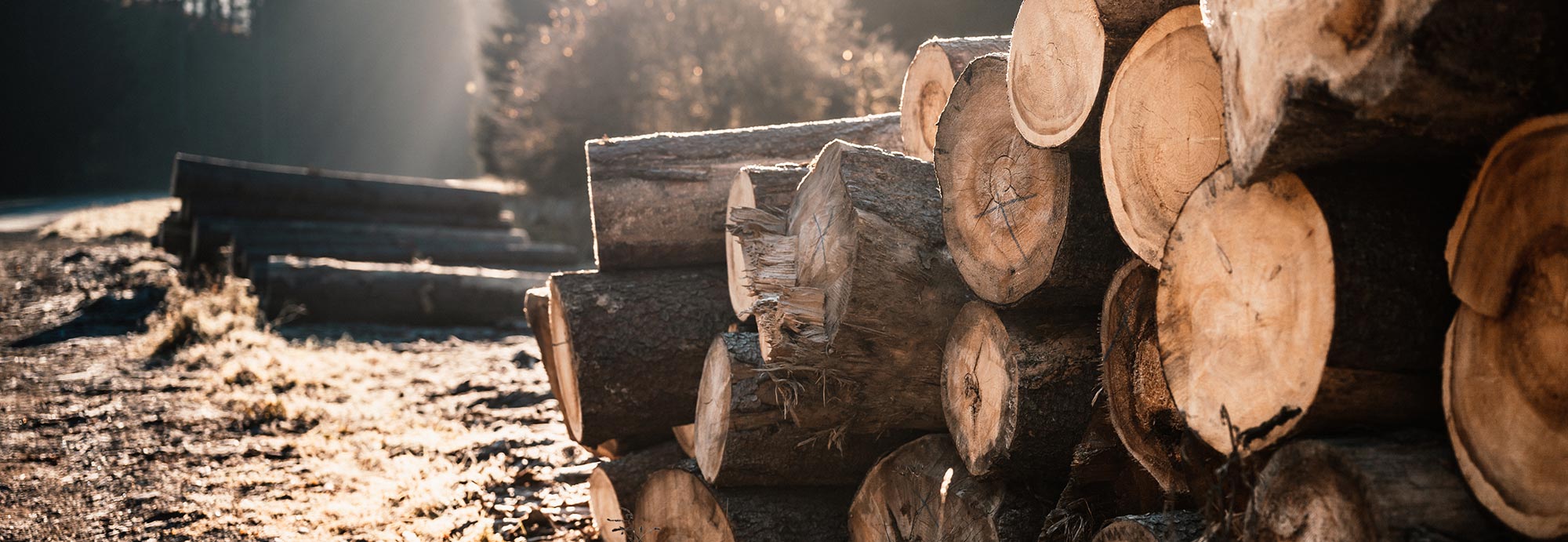
Intellinova online systems
Portable instrumentation
HD Technologies
Airius wireless sensors
Reliable condition monitoring solutions for optimized production
We offer patented and well-proven technologies for condition monitoring of rotating machinery with exceptional pre-warning times. Our product range includes online systems, portable instrumentation, wireless solutions, and accessories specifically designed for detecting misalignment, gear and bearing problems, balance issues, and more.
Vibration levels, temperature spikes, lubrication condition, and process-related signals, such as vibration relating to rotational speed rather than mechanical issues, are all efficiently monitored.
Data transfer possibilities enable integration into CMMSs, process control systems, and IoT platforms.
Robust installations withstand dusty, hot, and humid environments. For use in potentially explosive atmospheres, ATEX-compliant equipment is also available.