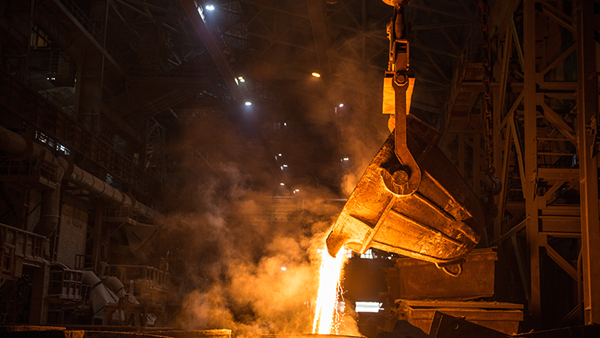
Rolling element damage in charging crane
Aiming to improve equipment reliability, a Russian steelworks initiated a pilot project where the Intellinova online system was installed to monitor the mechanical condition of a production-critical charging crane.
The crane, operating in the steel melting shop with an electric arc furnace, has an A+ criticality rating, and continuous operation is thus deemed vital to production. Multiple complicating factors, such as short measuring windows, fluctuating rpm, and varying loads, require the measuring system to have parallel measuring and triggering capability.
This case study describes the installation and configuration of the system and the detection of rolling element damage in a synchronizer bearing with five months’ prewarning time.
Download full case study
Case Study
CS031 - Charging crane - RUFilename/description | Language | Size | Modified | |
---|---|---|---|---|
CS_031B_Charging crane_RU.pdf | English (United Kingdom) | 18 MB | 1/19/2022 | |
The case study involves rolling element damage in a synchronizer bearing, detected five months before its replacement. |
Intellinova Compact
The high-performance Intellinova® Compact system is available in multiple versions, well suited for remote monitoring or industrial environments with groups of measuring points.
HD Technologies
High-definition condition monitoring technologies provide exceptional pre-warning times, maximizing the planning horizon for maintenance and repairs. In turn, this enables fully utilizing asset life, cutting repair costs, and minimizing the consequences of unplanned downtime.
Iron and steel
Condition monitoring is a cornerstone in the asset management of iron and steel plants. Having control of the operating condition is a must to optimize plant profitability.